
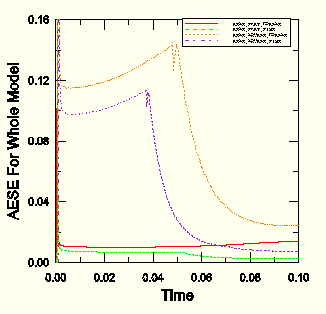
In this way, we benefit from the contact procedures and non-linear solver capabilities of ABAQUS in combination with the great advantages of X-FEM. We pre-process and post-process the information using Matlab as an interface. We use X-FEM embedded in ABAQUS via UEL, enabling the introduction of extra dof (this must be something very similar to what Xiujun Fang mentions above). under contact effects such as those due to square ended or cylindrical indenters).
#Abaqus strain energy output crack
We're modelling 2D crack propagation in fretting fatigue problems (i.e. I'm also of the opinion that ABAQUS capabilities are very powerful and are worth using. ENJOY THE BUMPY RIDE.:) and never lose hope. Please let me know if you require further clarifications.Īll the best. There are many criterion present, based on your explaination a criterion based on shear stresses might serve the purpose but not sure until further details of the experimental results are known. You might need many steps/increments etc. Another tedious way would be to find the potential direction of crack propagation and separate nodes in that direction but it is a tedious job to do. In most of the cases you must know the crack path apriori to perform crack propagation analyses in ABAQUS. Otherwise there is always a possibility to write a user material subroutine. Although, I am not sure if they are based on thermal loading or not. Please, have a look in the documentation and see if you find anyone of them useful. There are different material models already available in ABAQUS based on concrete cracking, damage plasticity, etc. selection of approperiate material model for the material, and identify or obtain the corresponding material parameters (most likely from experiments or literature search). construction of an optimized finite element model with proper assumptions of loading, boundary, symmetry, etc conditions and size, type of elements. You might know already about them but as starting point, basic ingredients of the cracking behaviour would be: Nature does not care whether you can describe a phenomenon by an equation. Breath taking and sometimes frustrating, i would say.:) I still remember those days when i was using cohesive model in simulating interface fracture. Mesh-independent discrete numerical representations of cohesive-zone models , Engineering Fracture Mechanics, Volume 73, Issue 2, January 2006, Pages 160-177 To remove mesh bias and predict a crack path with cohesive zone model, following reference may be of interest to people using cohesive models and stuck due to mesh bias. Simulation of cup–cone fracture using the cohesive model Engineering Fracture Mechanics, Volume 70, Issue 14, September 2003, Pages 1943-1961

One way of removing the mesh bias is to use cohesive elements everywhere but it is a tedious job and many problems regarding stability and convergence.:) Cohesive zone modelling always have some disadvantages as discussed by Yanfei and others.
